SOLUTIONS
Technology that is ideal for today’s hydrogen demand and tomorrow’s.
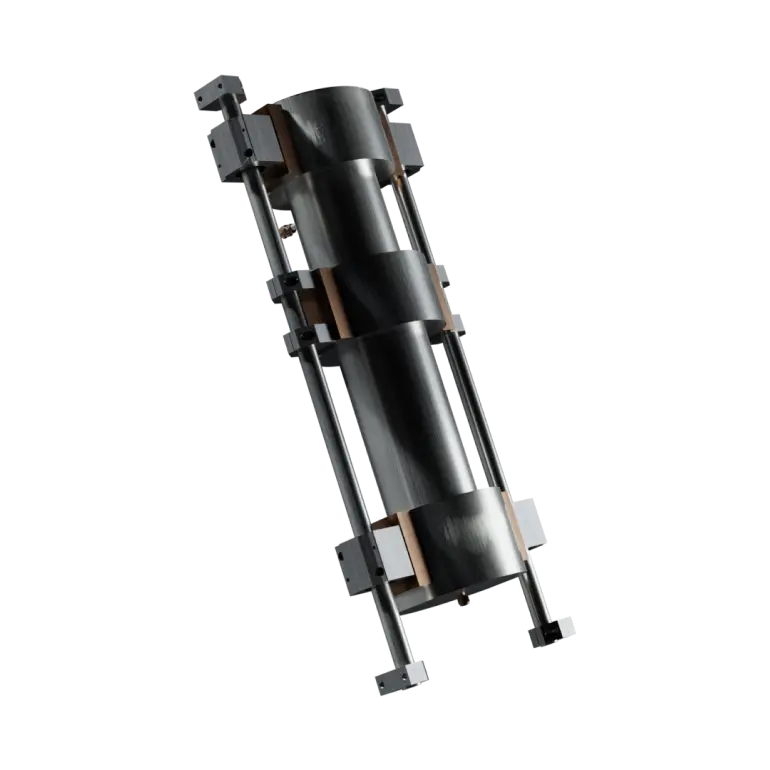
THE OPPORTUNITY
21%
*Levelised cost of hydrogen delivered above 200bara
20-30%
50%
17%
0
10x
Over 90% of the world’s hydrogen demand today requires hydrogen at pressure.
Industries like ammonia production, refineries and methanol production all require pressure in their chemical processes. Grey and green hydrogen production systems alike rely on unreliable and expensive hydrogen gas compressor systems to achieve this.
Hydrogen forms the lightest and least dense gas on the planet and it’s extremely explosive.
It is really hard to compress, requiring huge amounts of energy and complex fast moving hydrogen gas compressors that need to be designed with special materials and lubricants to ensure safety. Due to the risks, downtime is commonplace. High levels of redundancy are built into chemical plants that require high up-time and this multiplies the cost several-fold. These pieces of kit are an operator’s nightmare!
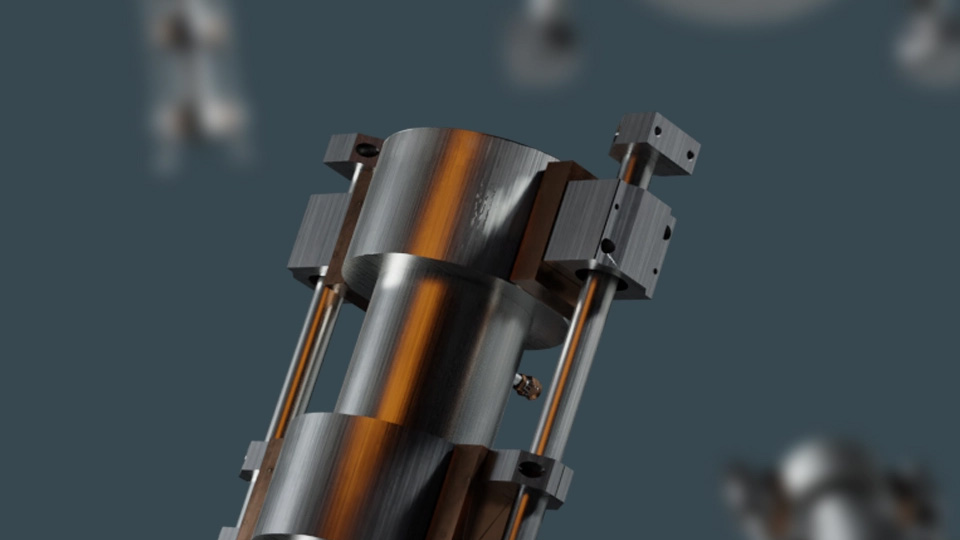
Supercritical has developed an electrolyser technology that negates the need for compressor systems entirely for today’s largest markets.
By increasing the pressure of the water going in, rather than compressing the gas coming out, we are able to produce high pressure hydrogen and oxygen much more efficiently and safely. We deliver our customers the hydrogen they need at the pressure they need it.
Future markets for hydrogen such as industrial heat and transport will require high pressures too.
Markets
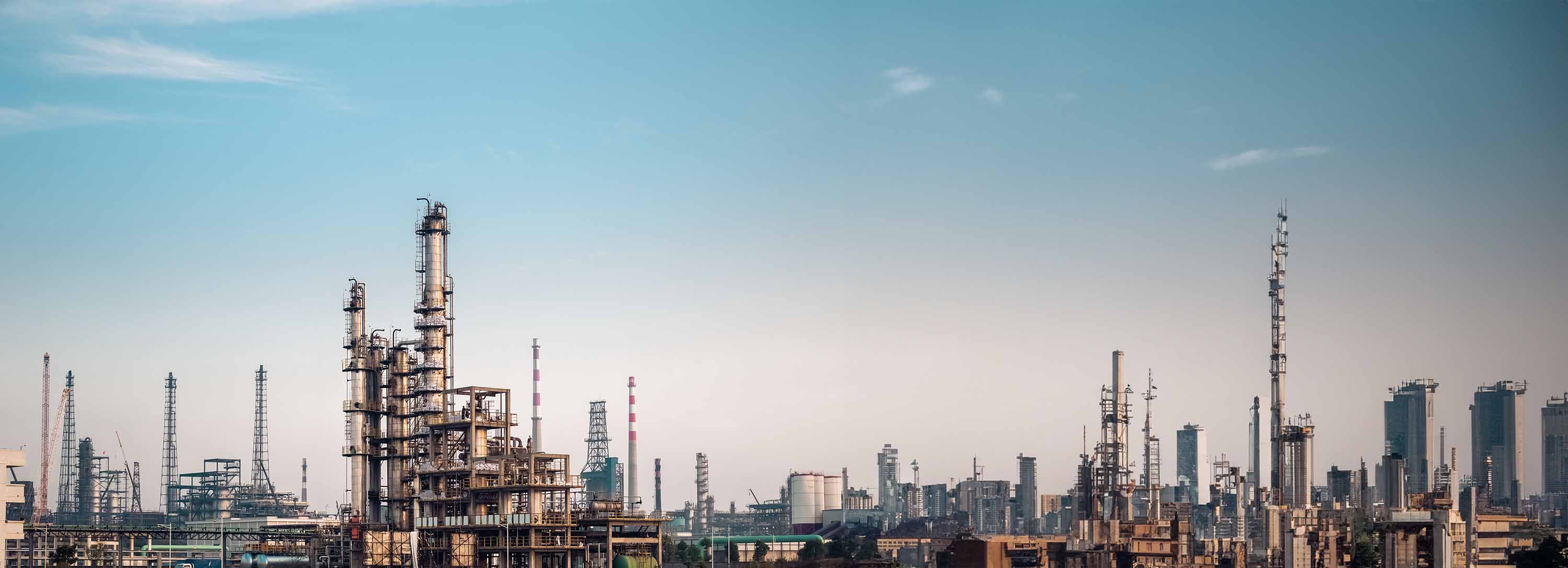
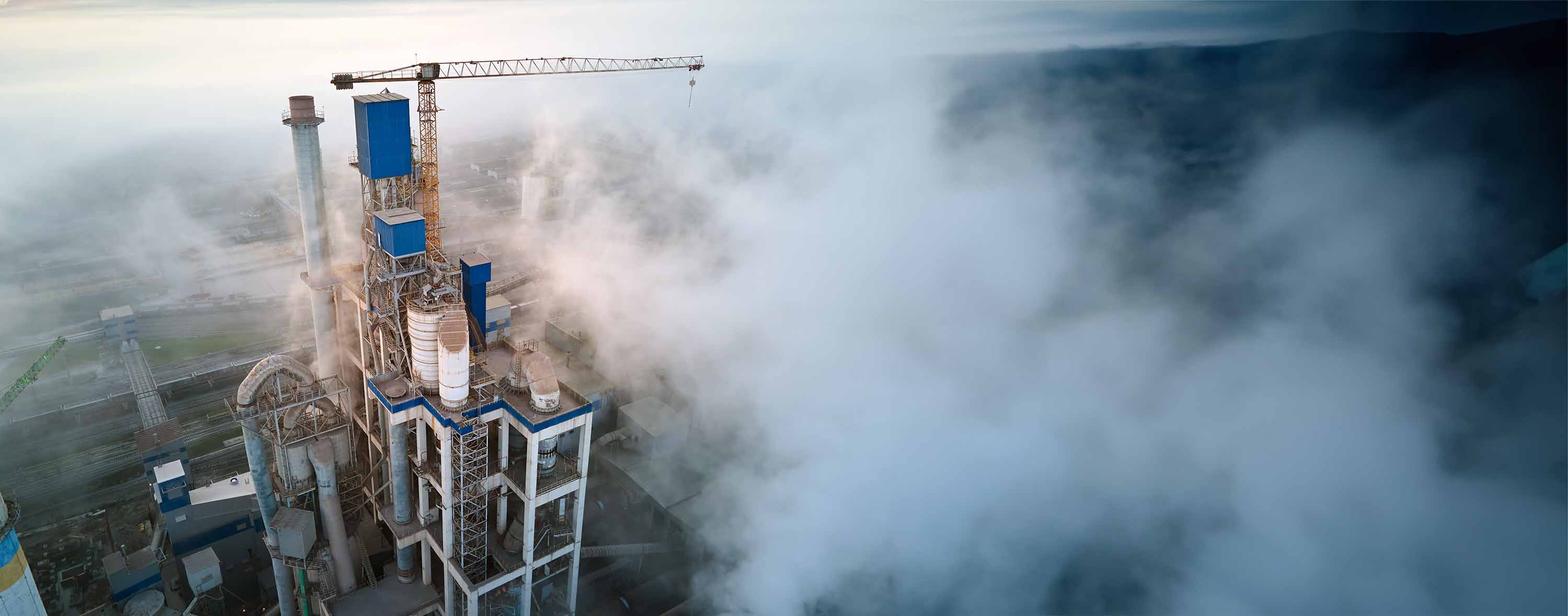
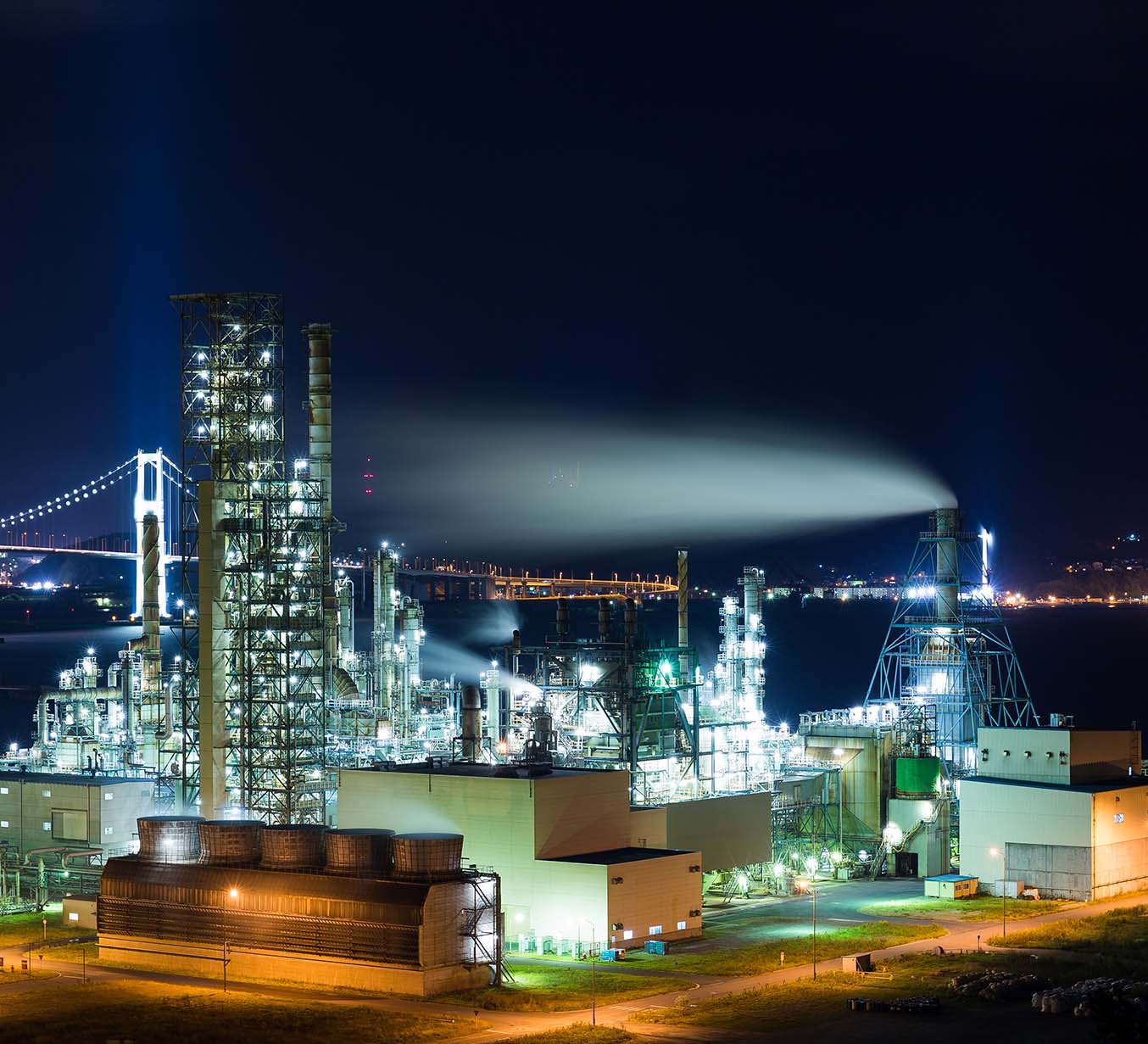
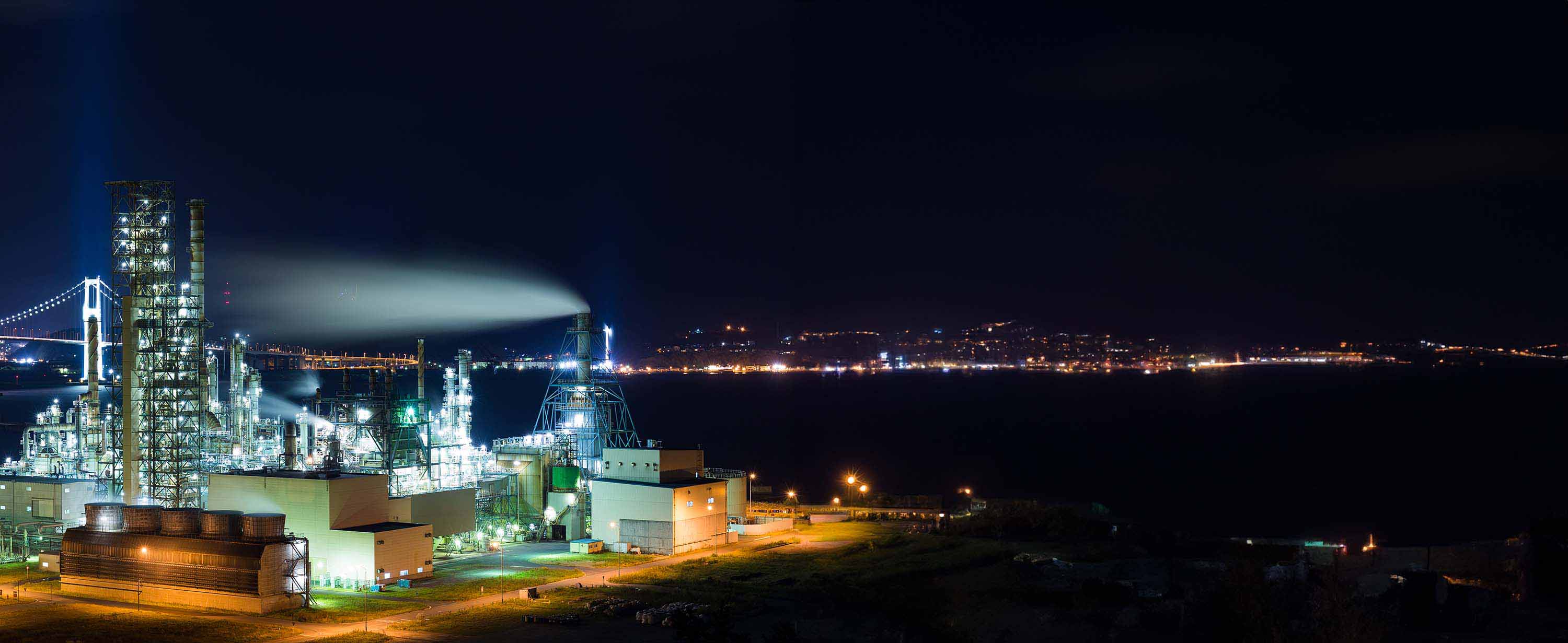
e-Chemicals
Today’s 90 million tonnes of hydrogen production serves three key markets:
- Ammonia (36% - for synthetic fertiliser production)
- Refineries (42% - for making more valuable and clean fuels)
- Methanol (15% - for chemical / polymer production)
This market in particular needs to decarbonise. Its resultant emissions due to its use of fossil fuels to produce hydrogen are in the region of 1 billion tonnes of CO2 per year. Even if all nascent applications of hydrogen utilisation did not take off, this market alone is a critical problem to solve to achieve net zero. Low cost, zero emission, high pressure hydrogen will be the tipping point to the shift.
Hydrogen from fossil fuels currently emits 1 billion tonnes of CO2 per year.
Ammonia production needs approximately 200bara delivery pressure and refineries and methanol production require between 50 and 150bara dependent on the unit operation, making Supercritical’s technology ideal for all existing markets.
Markets for hydrogen’s chemical properties are growing and multiplying. Fast.
Hydrogen is used in metal processes like nickel oxide reduction and has been for decades. The dial is about to be turned up to 11 in the metal sector however! Coal use remains a big part the steel industry, and a huge contributor to CO2 emissions and other pollutants. Hydrogen has the potential to displace coal due to its capabilities to reduce iron ore to iron.
A Hydrogen Europe study predicted that a typical primary steel plant in the EU would require 1.3GW of renewable powered electrolysers at 100% capacity factor. At a solar driven capacity factor, that rises to 5.0GW.
GreeNH3
We conducted a 9 month study with ScottishPower and Proton Ventures to evaluate the benefit that ultra-high efficiency, high pressure hydrogen production could offer to the burgeoning green hydrogen sector. By delivering at pressure, the ammonia plant can downgrade its compressor specification to a simple compressor. This reduces the cost by 10x! Going even further, taking hydrogen out of the compressor makes the compression significantly easier, reducing the duty by 75%.
In one fell swoop, Supercritical’s technology has massively reduced the cost of the most expensive element of the ammonia plant. What does this result in?
A 21% cost reduction versus incumbent green technologies.
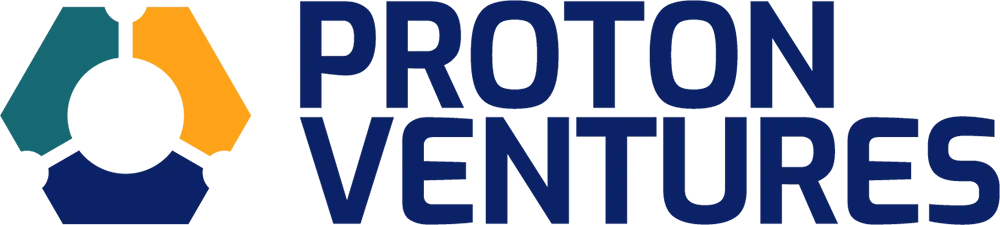
10X cost reduction
>200bara hydrogen delivery
21% lower LCOA than incumbent technology
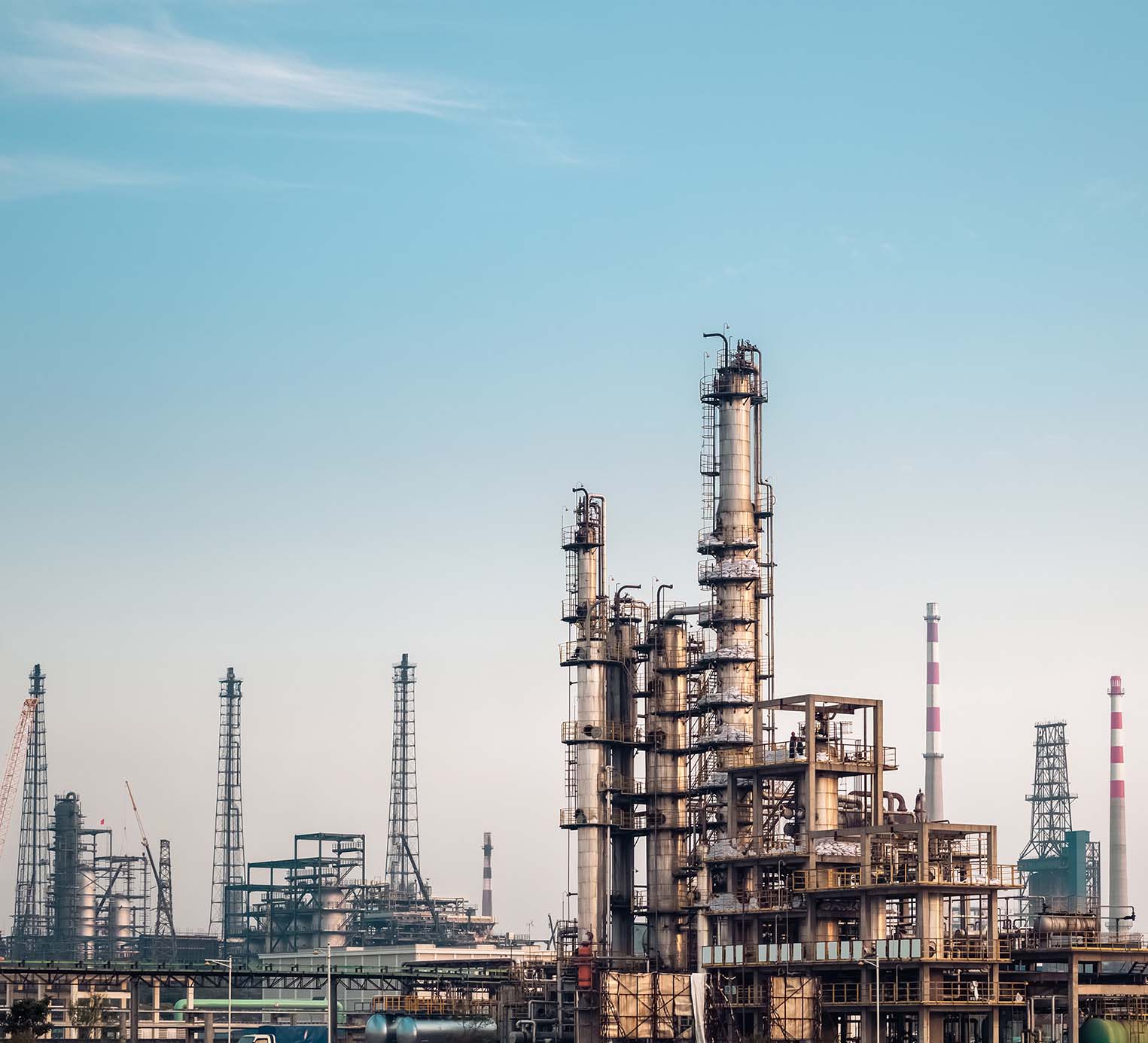
Net Zero Industrial Heat
19% of the world’s emissions are due to industries that operate with temperatures far exceeding those that can feasibly be electrified.
Using hydrogen for industrial heat means that you can hit the same temperature ranges as those hit with fossil fuels like natural gas whilst maintaining similar processes. Whilst similar, there are differences which are being verified in countless projects globally. Hydrogen burns hotter, hydrogen has different safety considerations, hydrogen is stored differently. Crucially, hydrogen can be combusted with no CO2 emissions.
We transitioned from biomass to coal. We transitioned from coal to oil. And we transitioned from oil to gas. Hydrogen is the next step in our energy evolution and it is limitless and sustainable when produced with renewable energy and water.
WhiskHy
As part of our WhiskHy project with Beam Suntory, a leading whisky producer globally, we had to ensure its 24/7 operation was undisturbed. The availability of renewables at the location had a capacity of 45% when considering a combined wind + solar solution. As that’s not 100%, it means that energy would need to be stored to enable the uptime required. By storing it at 200 bara, one can reduce the volume of storage required by 189x vs atmospheric storage. When considering the amount of space required for storage, this benefit is major.
Pressure will play a very important role in enabling the hardest to abate industrial heat players, like steel and cement, to decarbonise.
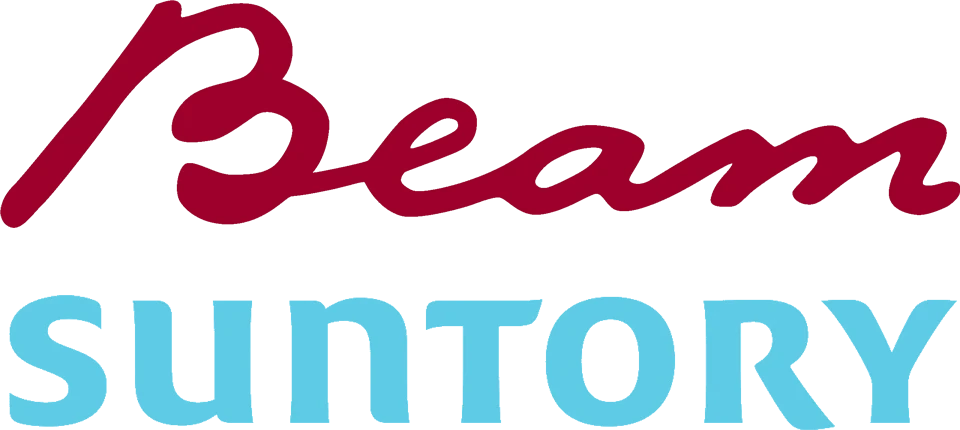
40% smaller electrolyser
£1.59 /kgH2
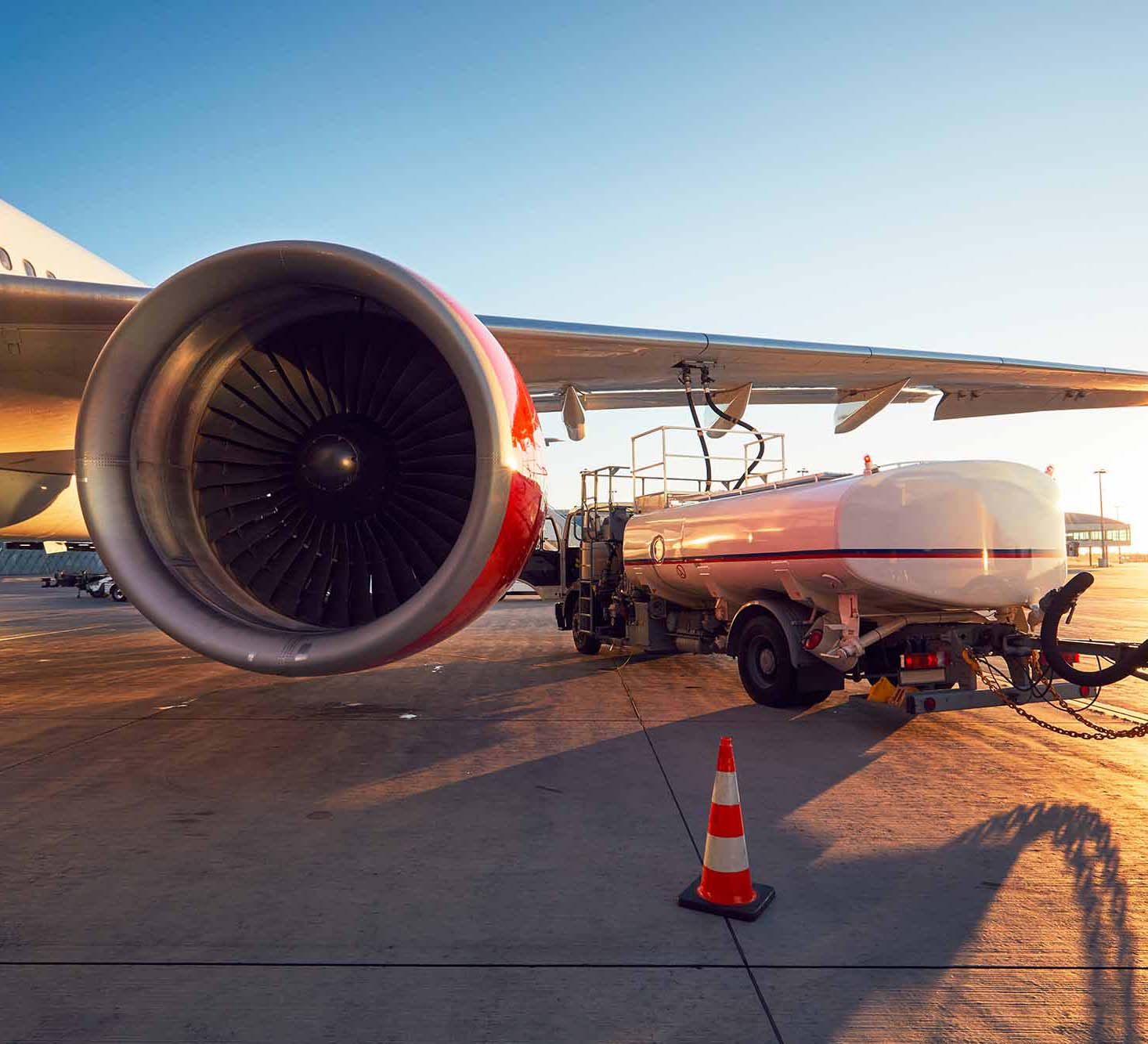
Emission Free Heavy Transport
In transport, hydrogen can be used as a fuel directly, in a fuel cell or an internal combustion engine. It is also a crucial feedstock to heavier fuels such as sustainable aviation fuel (SAF), methanol, ammonia and other e-fuels. It is an absolutely critical compound to decarbonise the transport sector. At Supercritical, we believe hydrogen will have a bigger role in bigger transport modes.
Hydrogen is a crucial feedstock to heavier fuels such as sustainable aviation fuel (SAF), methanol, ammonia and other e-fuels.
E-methanol and e-ammonia are leaders in marine transport decarbonisation plans. Sustainable aviation fuel and other e-fuels will play a major role in decarbonisation of planes and heavy transport in the future. Long chain hydrocarbons can be produced through chemical synthesis processes, converting CO2 (captured from the air) and hydrogen (made from splitting water) that mimic the fossil fuels that our lifestyles have become so accustomed to!
Zero Mining
We did a study with OZ Minerals, a modern mining company, now part of BHP, one of the largest mining companies in the world. We confirmed that in the case of high pressure fuel cell applications, typical low pressure electrolyser systems would require 10x more energy to compress to storage pressures of 350bara and would require 3 stages of compression and cooling compared to Supercritical’s 1 stage.
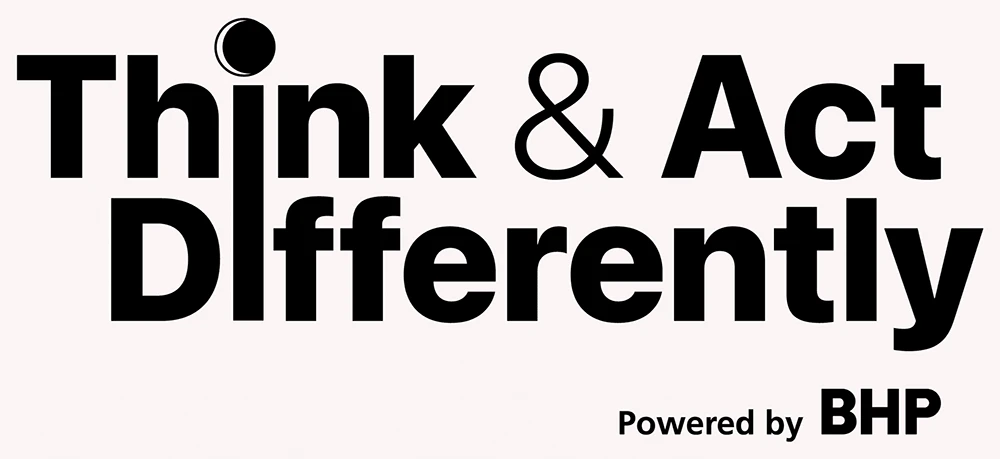